Field data capture – completing the circle
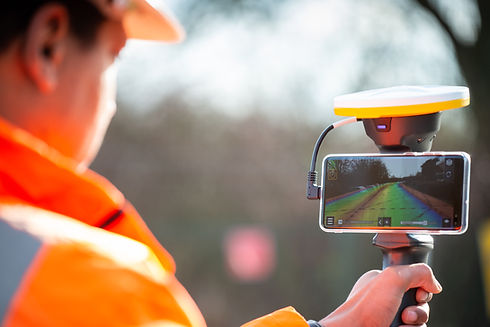
“Typically, to close a road and mark-out a 5km stretch of dual carriageway for defect repairs would take three shifts of 8 people and cost between £3k and £10k depending on the size of the job. Using KOREC Roadway functionality, we can now achieve the same amount of work in just one shift saving us around £20k on each 5km stretch.”
​
Michael Ambrose (Technical Lead on the National Highways Concrete Roads Programme)
Field data capture - Completing the circle
In our series of articles examining the trial and adoption of innovative digital technology by National Highways as part of their Concrete Roads Programme, we have already taken a close look at Mobile Mapping for large volume data collection and use of the online KOREC Portal for managing and sharing data. In this, our third article, we will be moving out of the office and back into the field to establish how National Highways has created a full circle of field/office digital data flow using KOREC’s Roadway field data capture system.
​
This handheld solution comprises a Trimble Catalyst GNSS (a low cost, on demand, cm accuracy GNSS) and KOREC Roadway (industry specific data capture software) running on a Trimble TDC600 rugged handheld. Three systems were purchased for use by National Highways supervisors during the trial.
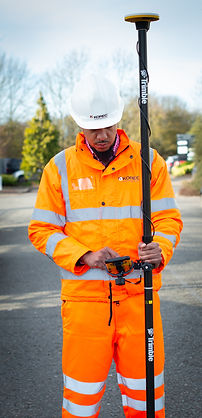
Trimble Catalyst GNSS used in conjunction with KOREC Roadway data capture software running on a Trimble TDC600 logger
Efficiency, digitisation and innovation
​
Putting an end to a pen and paper approach, National Highways required its new digital field data capture workflow to tie in with the project’s larger overall themes of greater efficiency, creativity and innovation as well as the more specific aims of a BIM modelling approach to road maintenance that would see their mobile mapping data populated with intelligent field-based information. This would provide them with scope for both greater efficiency in existing applications and the development of new and experimental ones.
​
The system was therefore developed to be fit for purpose in a number of ways: